Kemacetan truk di pabrik kimia merupakan masalah logistik yang signifikan, yang tidak hanya mengganggu produktivitas tetapi juga meningkatkan biaya operasional dan berpotensi merusak lingkungan. Masalah ini telah lama menjadi perhatian banyak pihak, baik itu pengelola pabrik, perusahaan pengangkut, maupun perencana sosial yang ingin mengurangi emisi dari kendaraan yang menganggur. Namun, kebanyakan solusi yang diusulkan cenderung menguntungkan salah satu pihak saja, tanpa mempertimbangkan kepentingan pihak lainnya. Hal ini menciptakan ketidakseimbangan yang memperburuk masalah.
Salah satu solusi yang sering digunakan adalah sistem janji temu truk (Truck Appointment System, TAS). Sistem ini mengatur waktu kedatangan truk untuk meminimalkan antrean dan kemacetan di area pabrik. Namun, meskipun beberapa pabrik telah menerapkan TAS, hasilnya seringkali kurang optimal karena pengaturannya hanya mempertimbangkan satu sudut pandang, baik dari pengelola pabrik atau perusahaan pengangkut saja. Selain itu, kebiasaan truk yang datang lebih awal dari jadwal untuk menghindari keterlambatan dalam waktu yang padat juga menambah masalah. Oleh karena itu, pendekatan yang lebih komprehensif diperlukan untuk mengoptimalkan penerapan TAS di pabrik kimia.
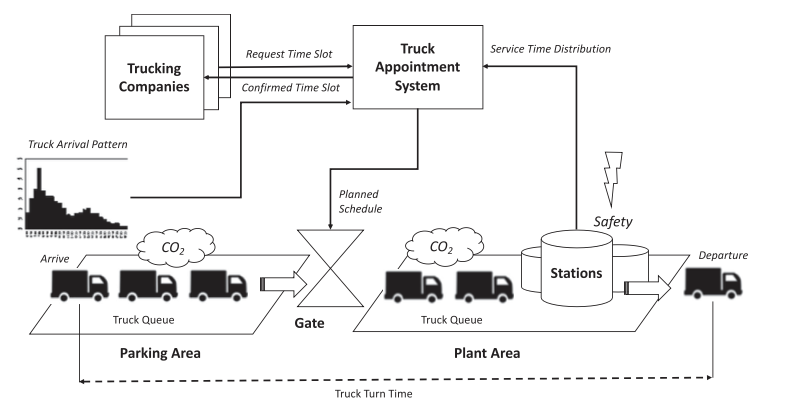
Penelitian yang dilakukan oleh Budhi Wibowo dan Jan Fransoo menawarkan solusi dengan mengusulkan model optimasi bersama (joint optimization) yang melibatkan semua pemangku kepentingan—pengelola pabrik, perusahaan pengangkut, dan pihak perencana sosial. Dengan pendekatan ini, peneliti berhasil menunjukkan bahwa dengan mempertimbangkan kepentingan setiap pihak, sistem TAS dapat lebih efisien dalam mengurangi waktu tunggu truk, mengurangi biaya operasional, serta mengurangi emisi yang dihasilkan dari truk yang menganggur.
Kontribusi utama dari penelitian ini adalah pengembangan model optimasi bersama yang mengakomodasi kepentingan berbagai pihak secara simultan. Berbeda dengan pendekatan sebelumnya yang hanya fokus pada salah satu stakeholder, penelitian ini mengintegrasikan tujuan masing-masing pihak ke dalam satu sistem yang lebih adil dan efisien. Sebagai contoh, pengelola pabrik lebih diuntungkan dengan berkurangnya waktu lembur karena penerapan TAS yang lebih efisien, sementara perusahaan pengangkut mendapat manfaat dari pengurangan waktu tunggu truk yang dapat meningkatkan produktivitas mereka.
Sebagai tambahan, penelitian ini juga mengembangkan metode baru untuk mengevaluasi kinerja sistem antrian dinamis, yang dikenal sebagai WB-PSFFA (Whitt-Bisection Pointwise Stationary Fluid Flow Approximation). Metode ini merupakan perbaikan dari metode sebelumnya, B-PSFFA, dengan menggabungkan prinsip aliran fluida dan pendekatan stasioner. Pengembangan metode baru ini adalah salah satu kontribusi penting penelitian ini, karena memungkinkan estimasi yang lebih akurat terhadap sistem antrian non-stasioner yang menggambarkan dinamika kedatangan truk yang bervariasi terhadap fungsi waktu. Dengan metode baru ini, peneliti dapat memodelkan kinerja TAS di pabrik kimia dengan lebih presisi, meskipun terdapat variasi dalam pola kedatangan truk sepanjang hari.
Implikasi manajerial dari temuan ini sangat penting bagi pengelola pabrik dan perusahaan logistik. Penerapan sistem TAS yang dioptimalkan bersama dapat mengurangi kemacetan di pabrik, meningkatkan efisiensi operasional, dan pada saat yang sama mengurangi emisi karbon yang dihasilkan oleh kendaraan. Dari perspektif pengelola pabrik, hal ini berpotensi menurunkan biaya terkait operasional dan meningkatkan produktivitas. Sementara itu, perusahaan pengangkut dapat merasakan manfaat dari berkurangnya waktu tunggu truk yang berdampak langsung pada penghematan biaya dan peningkatan efisiensi.
Namun, penerapan model ini bukan tanpa tantangan. Pengelola pabrik dan perusahaan pengangkut harus saling berbagi informasi mengenai pola kedatangan truk dan waktu pelayanan yang sebenarnya agar optimasi dapat berjalan dengan lancar. Selain itu, peran perencana sosial, seperti pemerintah, juga sangat penting untuk memastikan bahwa sistem ini dapat berjalan tanpa menambah beban sosial atau lingkungan.
Secara keseluruhan, penelitian ini memberikan wawasan baru mengenai pentingnya kolaborasi antar pemangku kepentingan dalam mengoptimalkan sistem logistik di pabrik kimia. Meskipun belum sepenuhnya terimplementasi secara luas, hasil dari penelitian ini menunjukkan bahwa optimasi bersama dapat membawa manfaat yang lebih besar bagi semua pihak yang terlibat. Sebagai langkah selanjutnya, perlu ada kolaborasi yang lebih erat antar stakeholder serta eksperimen lebih lanjut untuk menyesuaikan sistem dengan dinamika nyata di lapangan.
Sumber: Wibowo, B., & Fransoo, J. (2021). Joint-optimization of a truck appointment system to alleviate queuing problems in chemical plants. International Journal of Production Research, 59(13), 3935-3950.
Disclaimer: Sebagian konten dalam tulisan dikembangkan dengan bantuan teknologi kecerdasan buatan (AI) dari platform OpenAI ChatGPT. AI digunakan untuk mengkonversi artikel ilmiah yang merupakan karya asli penulis ke dalam bahasa artikel populer. AI juga digunakan untuk membuat ilustrasi pada kepala tulisan. Gambar lain merupakan karya asli penulis. Penulis tetap melakukan pengecekan dan pengeditan atas semua konten untuk memastikan akurasi, relevansi, serta kesesuaian dengan sumber aslinya.